Three aviation engineering workshops, each unique in their own way, agree that open communication is at the heart of their approach to safety.
Vector spoke to senior personnel at three different aviation engineering workshops to follow up on the Vector (Winter 2024) article, Engineers’ mental health – from stress to strength.
We wanted to explore how a strong safety culture can support aviation maintenance engineers to thrive in a highly challenging environment.
We found common themes useful to any aviation maintenance company if they want to improve.
It’s safe to speak up
All three companies stressed the importance of creating an environment where people feel safe to speak up, disagree openly, and to bring up concerns without repercussions or pressure to sugarcoat bad news. In other words, creating psychological safety.
“You know you’re getting quality feedback from the staff because it sounds a lot like complaining,” says Jeremy Booth, the Chief Executive of Performance Engineering in Wānaka (and Safety Manager at Skydive Wānaka).
“The staff don’t say, as they might in a more ‘corporate’ environment, ‘Here’s an opportunity’. They say, ‘This isn’t right, it’s annoying me’.
“Don’t shut down the ‘complaining’. Listen closely, be willing to learn and find value in criticism. Then move the issue into the safety management system so you can track it.”
He’s certain this open style of communicating is helping to drive safety reporting. He says it’s vital, however, that communication is a “two-way street”.
“When people report safety concerns, we need to let them know how it’s being dealt with. Unless we link the two, there’s a gap between the value people see in participating in the safety management system, and what happens as a result.”
Grant Stewart, the Safety Manager at HeliSupport in Wānaka, says open communication needs to extend to all parts of the organisation if it’s going to be effective in creating psychological safety.
“Our owners, Jason and Kelly Buick, are hands-on, on the floor and talking to everyone from the chief engineer to our apprentices.
“People will speak up if the company has a robust just culture. This can mitigate ‘resident pathogens’ that, when triggered, can lead to an incident or accident.”
Grant adds that Jason and Kelly don’t just talk, they muck in and help. This is a positive piece of communication in itself.
“Everybody’s looking after everybody else. We have 30 people, but we’re really close-knit.”
At aircraft manufacturers NZAero in Hamilton, the Chief Pilot and General Manager of Engineering, Ray Long, says when something goes wrong, “Our people can tell me what’s happened, then we can deal with it and get it fixed”.
He adds when people know that issues are dealt with calmly, they’re “more likely to come and talk to me when they have a problem.
“If you don’t get mad, but stay measured when something goes wrong, they’re more likely to come and speak to you in other situations.”
There’s a team of 40 on the manufacturing side of the business, but Ray says it’s not hard to identify when someone’s feeling a bit off, even if they haven’t spoken about it.
“I’ll go to them and ask whether everything is okay, if there’s anything they need, if there’s any way we can help.”
Preventing undue influence
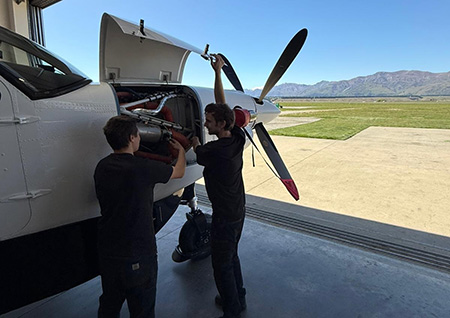
Photo courtesy of Performance Aviation
Engineers feeling pressured by operators and clients was a strong theme in the winter Vector article on mental health.
Jeremy, Grant, and Ray describe measures they have in place to avoid undue influence in the first place, and deal with it promptly if it arises.
Scheduling work in advance, and communicating clearly with customers about time frames, are essential practices.
At Performance Aviation, Jeremy says they have a new booking system helping them to forecast workflow for the year.
“We look at regular customers, and how often their aircraft will come in, and apply that to our forecasts. Then we look at big calendar items, such as engine overhauls. We let customers know our turnaround times, especially if they want us to do the work when we’re busy.”
The customers and their agents, when they visit, remain in a different part of the building from the engineers.
“At times, when a pilot is waiting in the vicinity of an engineer working on their aircraft, we’ll invite the pilot to go and have a coffee or wait in the lunchroom, to remove that pressure from our team.”
At NZAero, Ray Long says external client pressure isn’t an issue for the manufacturing team, but as General Manager of Engineering he’s careful to avoid putting any sort of pressure on their quality control personnel.
“It’s deliberately a standalone operation, so they’re in a position to make recommendations without undue influence from me.
“There are plenty of times when I’ve thought, ‘Just make a decision – is it within tolerances or not?’ But I’ve got to bite my tongue and let the process run its course.”
At HeliSupport, which is an Airbus and Safran Service Centre, Grant Stewart says, “The engineering manager and workshop foremen are responsible for making sure commercial pressures don’t reach the engineers on the shop floor.”
Good forward planning, airworthiness meetings, strict contractual obligations, and efficient parts procurement are also essential ways of front-footing customer expectations and managing workflow.
“The largest risk is problems with parts procurement. That’s what causes aircraft to stay on the ground. We don’t want our customers to have aircraft on the ground, and we don’t want our engineers to be working all hours to get them airworthy.
“We have to be very sharp around our approved supplier register, and we have to make sure we have a good supply of regularly needed parts.”
Avoiding and managing fatigue
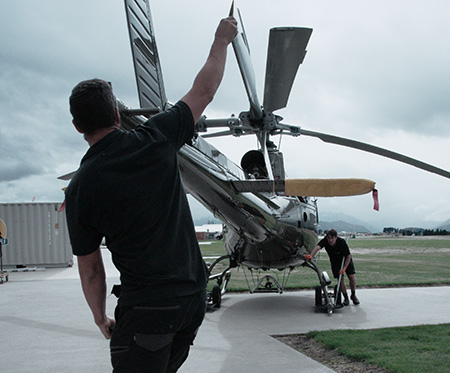
Photo courtesy of HeliSupport
Fatigue is a well-established factor in maintenance engineering incidents globally.
Jeremy, Grant, and Ray all say the scale of their companies, and their ability to spread task load, are essential for avoiding and managing fatigue.
At HeliSupport, Grant says they’re big on sticking to duty times, and they don’t do night shifts or work on weekends.
HeliSupport pilots and maintenance engineers travel to Antarctica to support international logistics and operations. They’re well-versed in the impact of 24-hour daylight on circadian rhythms before they go. They also have to manage the challenges of living in a small container with other people for months at a time.
Grant says he keeps a careful watch on staff who travel over “the hill” every day from Queenstown to the HeliSupport base at Wānaka Airport. He sees spikes in fatigue when winter driving conditions are bad.
Workers with young families can suffer from disturbed sleep, as can staff sharing flats in Queenstown with hospitality workers who come home from their shifts at different times of the night.
“In our Monday morning meeting, we talk about fatigue and mental health because they have a significant effect on safety.”
Jeremy Booth says Performance Aviation has approached the risk of fatigue in several ways. One is to invest heavily in upskilling their staff with qualifications and ratings. This increases the pool of those who are qualified to work on and supervise jobs, and helps to spread the load.
“We’re lucky that we’re part of a bigger organisation. We can bring one or two engineers over from Australia if we’re really busy. They’ve got a similar working culture and that’s been really beneficial.”
He says the scale of their operation in Wānaka also means their engineers don’t carry all the burden of ordering parts, checking CAA rules, and putting work packs together. They have other staff who do that.
Caring about people
Jeremy, Grant, and Ray all discussed ways they take care of their people, not just because it’s the right thing to do, but also because it’s a smart business move.
At HeliSupport, for example, the company lays on free lunch twice a week for the staff. It’s even cooked by a chef.
“It’s quite a big thing,” Grant says. “You don’t want your people being hungry, and we’re 15 minutes outside Wānaka so there isn’t much access to good food during the day.”
Excellent induction processes, paying their people well, and enabling their staff – including their apprentices – to advance within the company, are also high priorities.
“You get to be a market leader because people want to work with you,” Grant says.
Ray Long says the shifts at NZAero are timed so the staff finish at 2pm on a Friday, giving them time to do life admin – getting a warrant for their car, or whatever it may be – so their weekends aren’t taken up with those tasks.
Jeremy Booth says, “We all have lives outside work, so we’re as flexible and considerate as possible with work hours for our staff, to help out when we can. A happy team is a cornerstone of good culture.”
Footnote
Main photo courtesy of HeliSupport